General Information
- Leveraging Reward Consistency for Interpretable Feature Discovery in Reinforcement Learning
- Qisen Yang, Huanqian Wang, Mukun Tong, Wenjie Shi, Gao Huang, and Shiji Song
- Tsinghua University, China
- Q. Yang, H. Wang, M. Tong, W. Shi, G. Huang and S. Song, "Leveraging Reward Consistency for Interpretable Feature Discovery in Reinforcement Learning," in IEEE Transactions on Systems, Man, and Cybernetics: Systems, vol. 54, no. 2, pp. 1014-1025, Feb. 2024, doi: 10.1109/TSMC.2023.3312411.
Leveraging Reward Consistency for Interpretable Feature Discovery in Reinforcement Learning
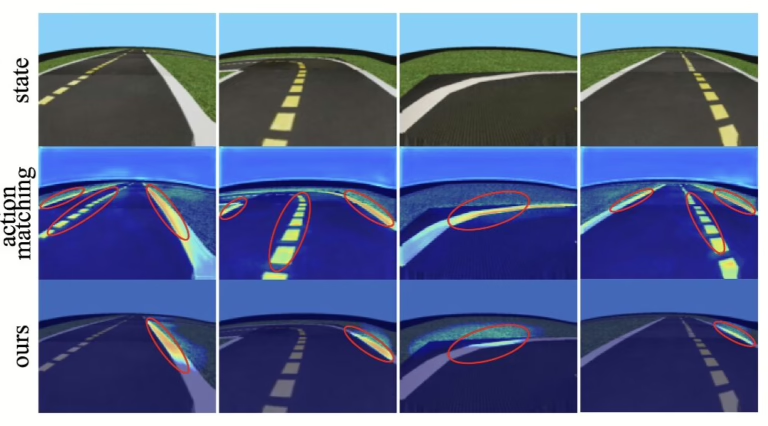
What is interpretable feature discovery in reinforcement learning?
To understand this, let’s introduce a few important topics:
Reinforcement Learning (RL): A machine learning approach where an agent gains the ability to make decisions by engaging with an environment to accomplish a specific objective. Interpretable Feature Discovery in RL is an approach that aims to make the decision-making process of RL agents more understandable to humans.
The need for interpretability: In real-world applications, especially in safety-critical domains like self-driving cars, it is crucial to understand why an RL agent makes a certain decision. Interpretability helps:
- Build trust in the system
- Debug and improve the model
- Ensure compliance with regulations and ethical standards
- Understand fault if accidents arise
Feature discovery: Feature discovery in this context refers to identifying the key artifacts (features) of the environment that the RL agent is focusing on while making decisions. For example, in a self-driving car simulation, relevant features might include the position of other cars, road signs, or lane markings.
Learn about RL, navigation, and other robot autonomy topics at the link below!
Abstract
The black-box nature of deep reinforcement learning (RL) hinders them from real-world applications. Therefore, interpreting and explaining RL agents have been active research topics in recent years. Existing methods for post-hoc explanations usually adopt the action matching principle to enable an easy understanding of vision-based RL agents. In this article, it is argued that the commonly used action matching principle is more like an explanation of deep neural networks (DNNs) than the interpretation of RL agents.
It may lead to irrelevant or misplaced feature attribution when different DNNs’ outputs lead to the same rewards or different rewards result from the same outputs. Therefore, we propose to consider rewards, the essential objective of RL agents, as the essential objective of interpreting RL agents as well. To ensure reward consistency during interpretable feature discovery, a novel framework (RL interpreting RL, denoted as RL-in-RL) is proposed to solve the gradient disconnection from actions to rewards.
We verify and evaluate our method on the Atari 2600 games as well as Duckietown, a challenging self-driving car simulator environment. The results show that our method manages to keep reward (or return) consistency and achieves high-quality feature attribution. Further, a series of analytical experiments validate our assumption of the action matching principle’s limitations.
Highlights - Leveraging Reward Consistency for Interpretable Feature Discovery in Reinforcement Learning
Here is a visual tour of the work of the authors. For more details, check out the full paper.
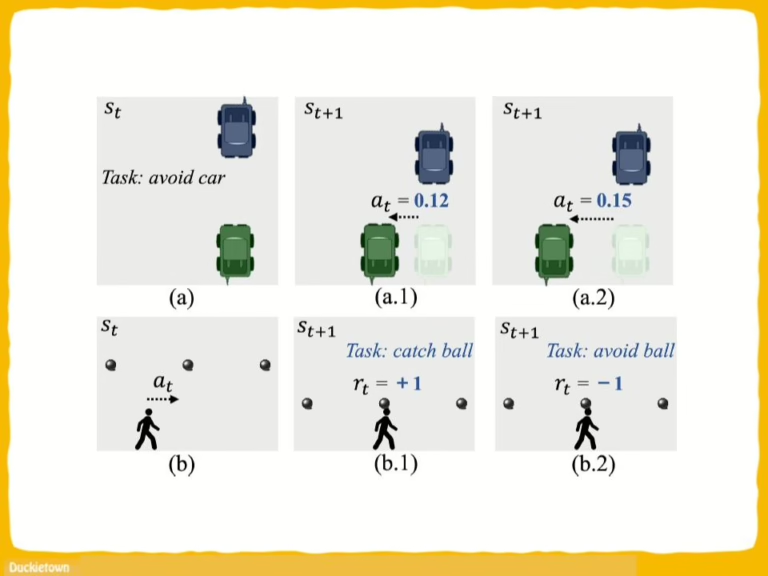
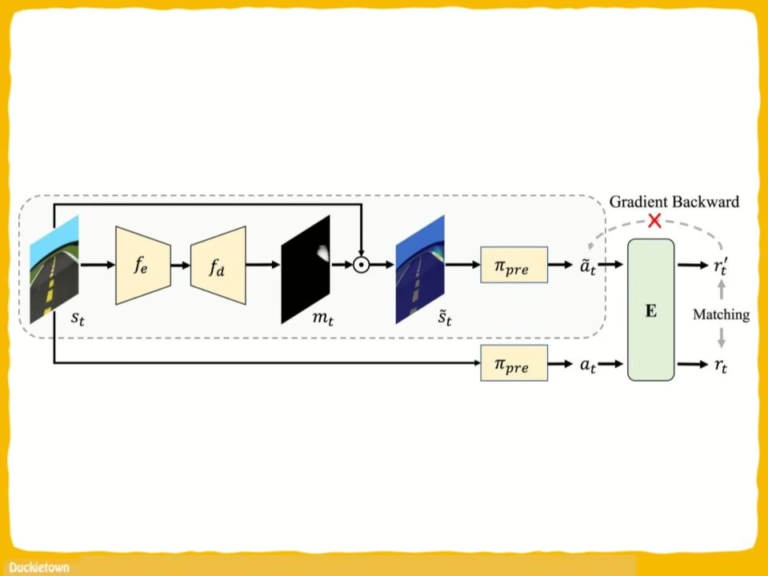
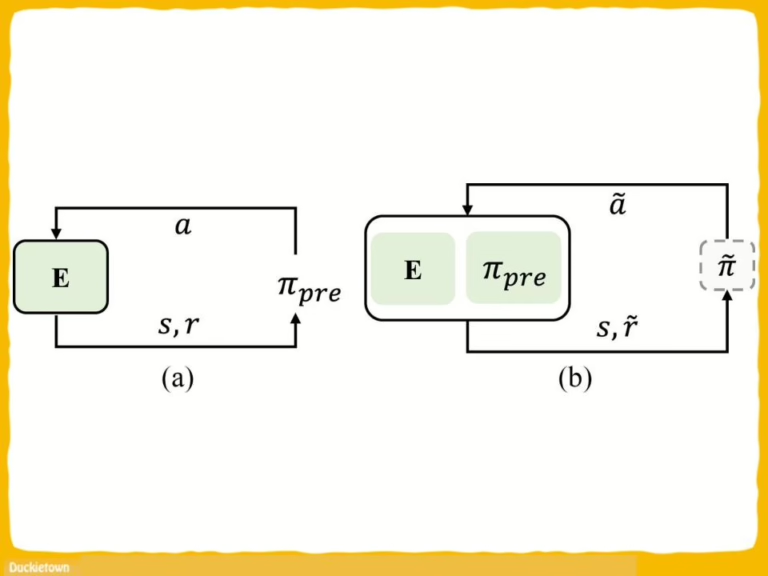
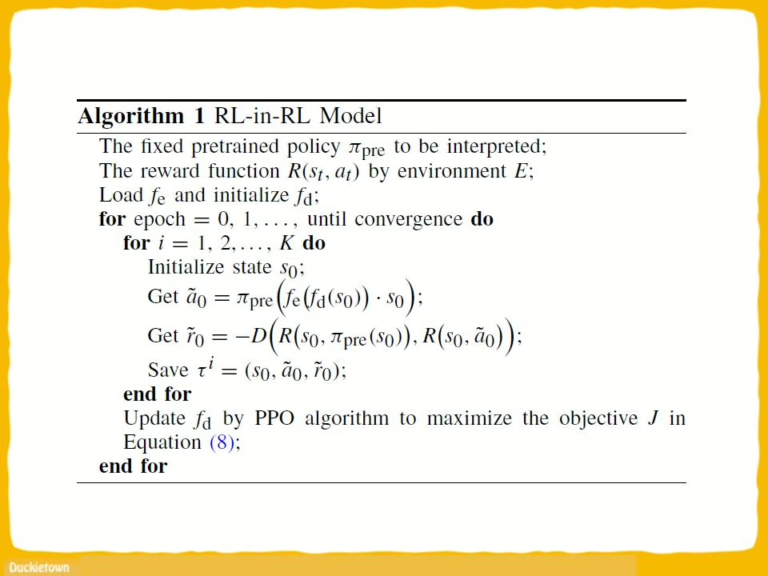
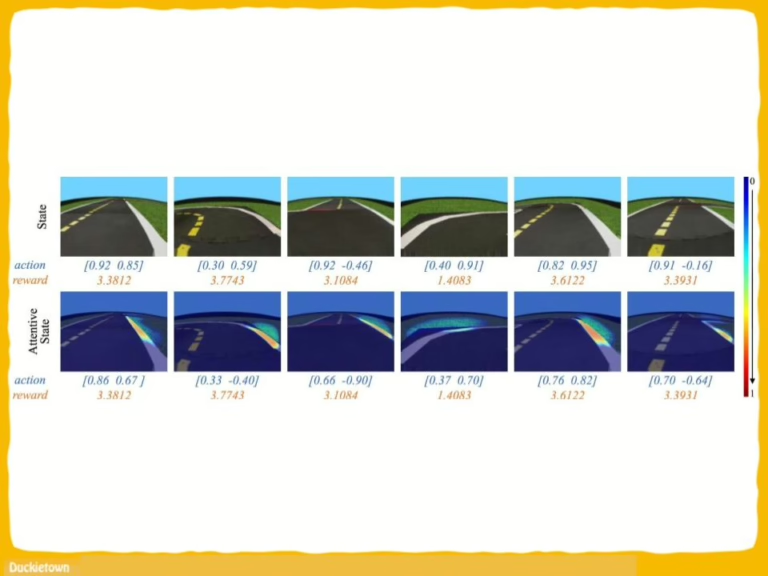
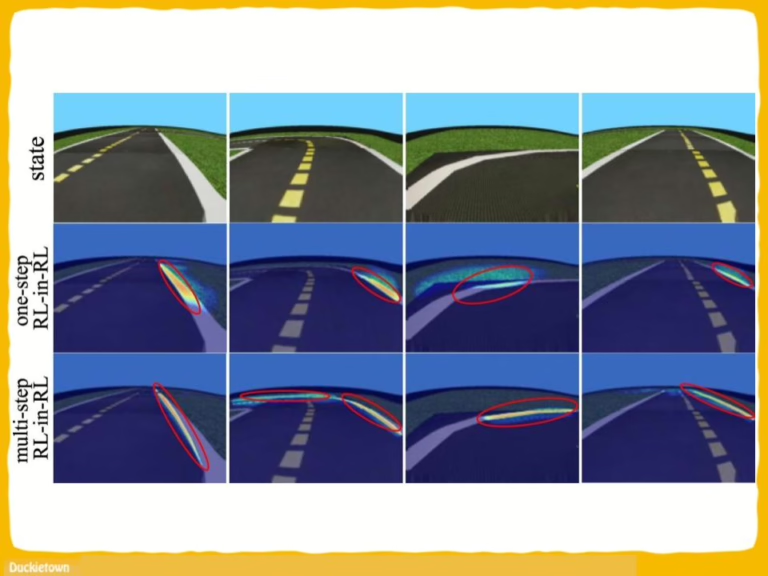
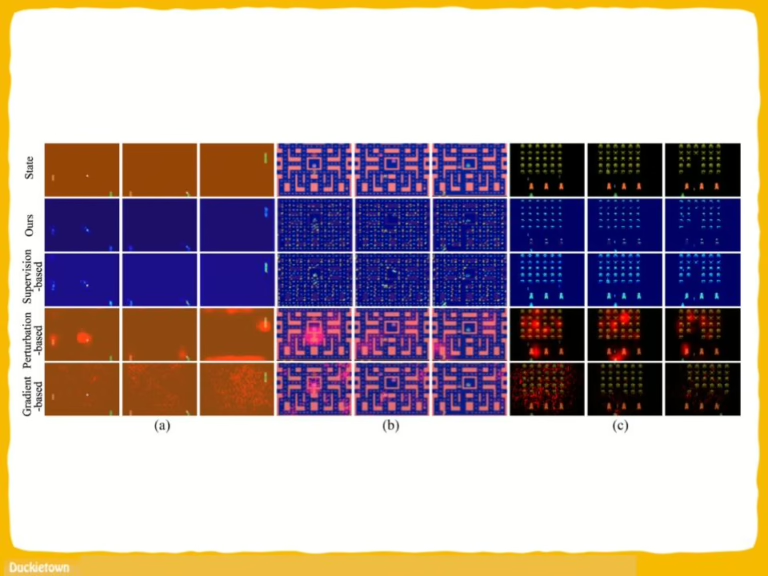
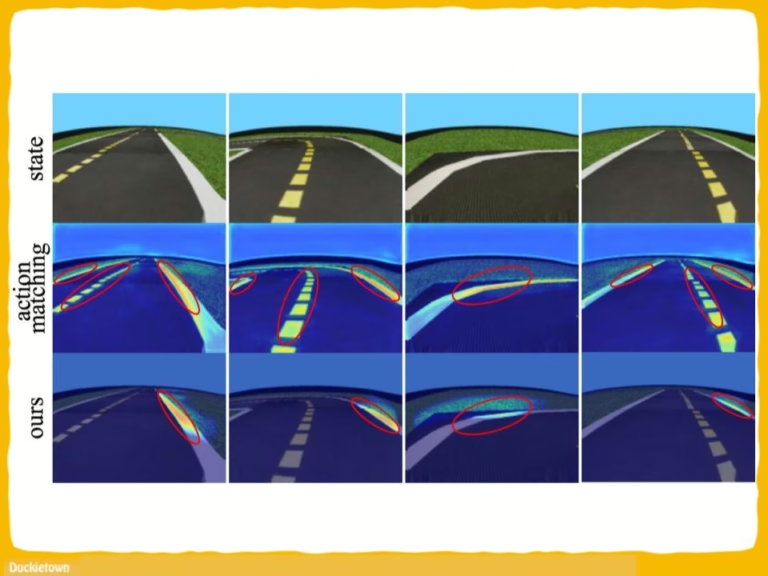
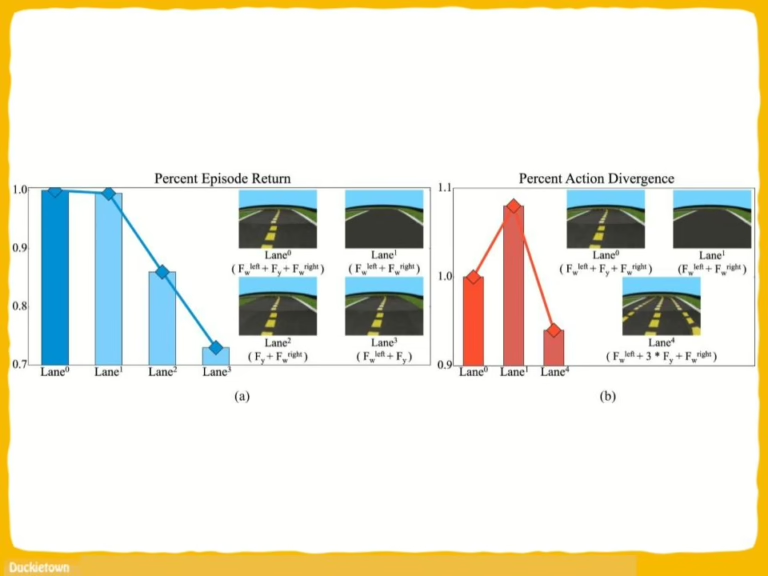
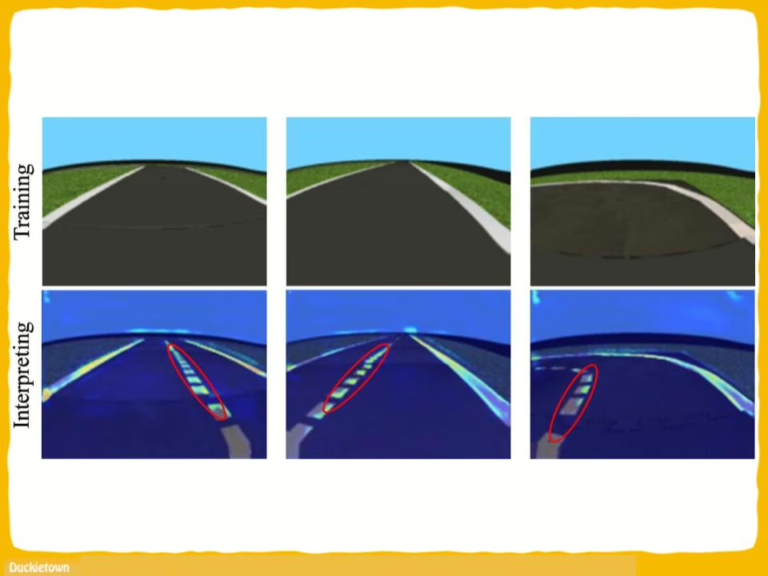
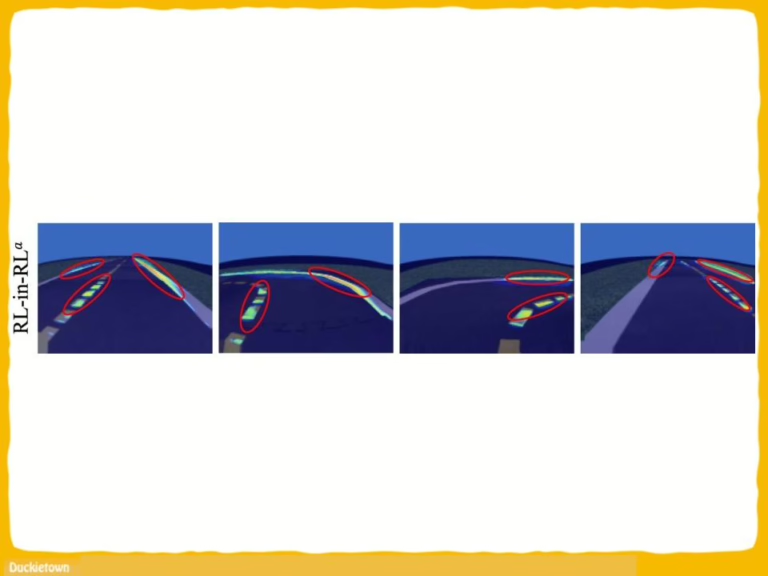
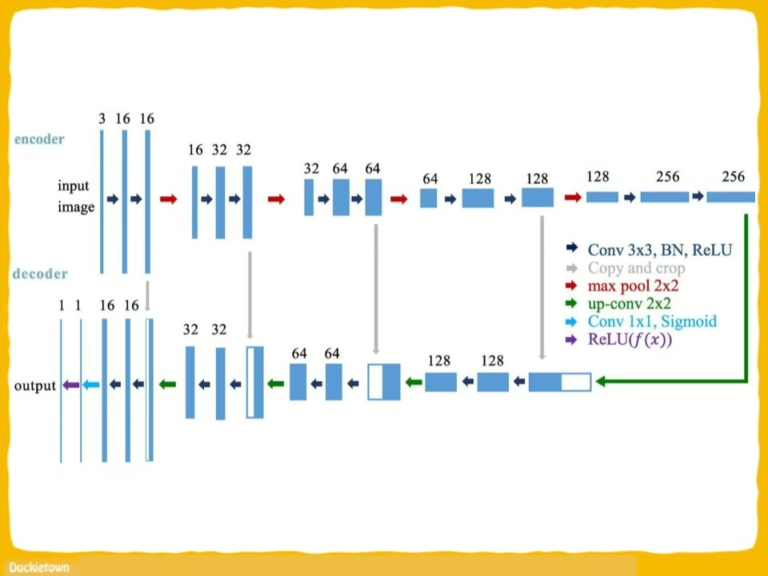
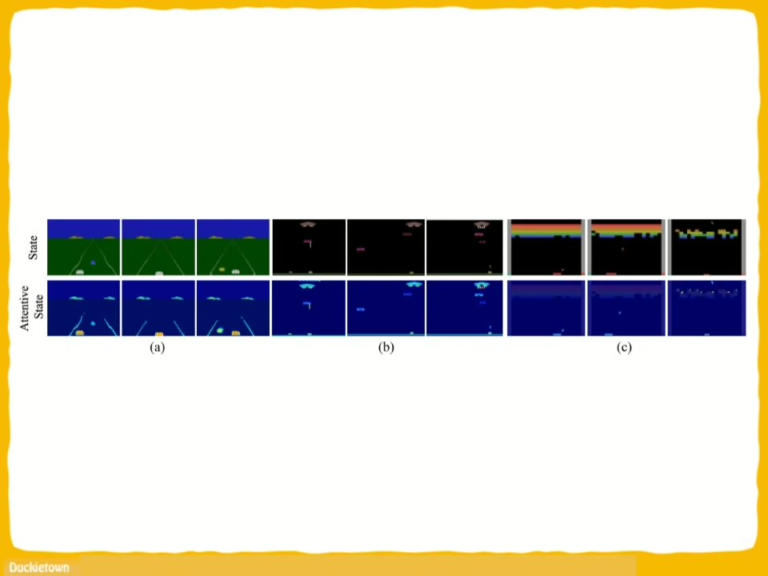
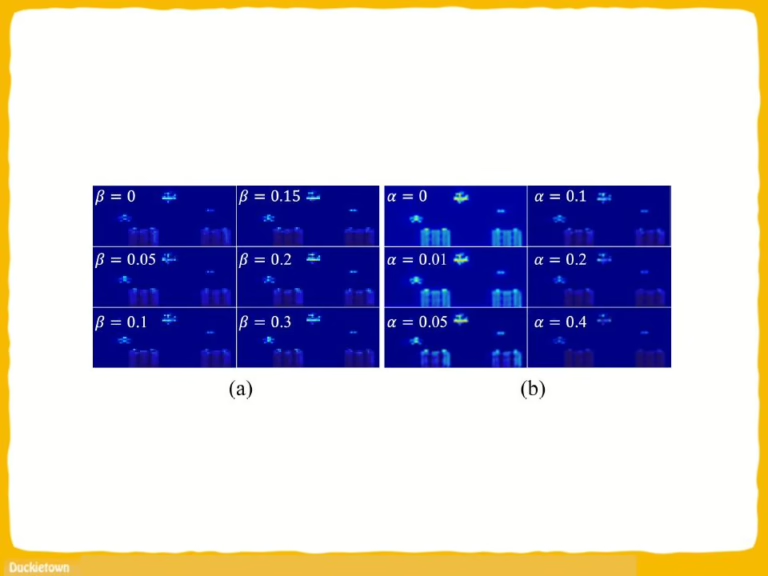
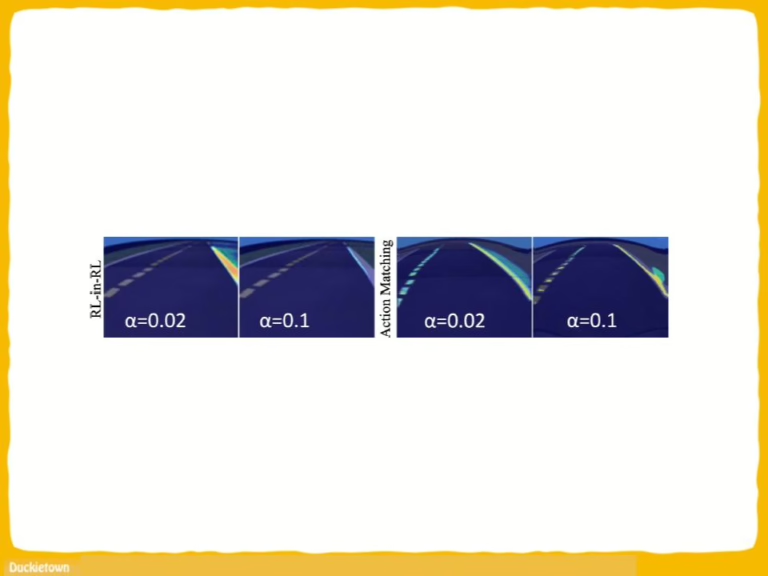
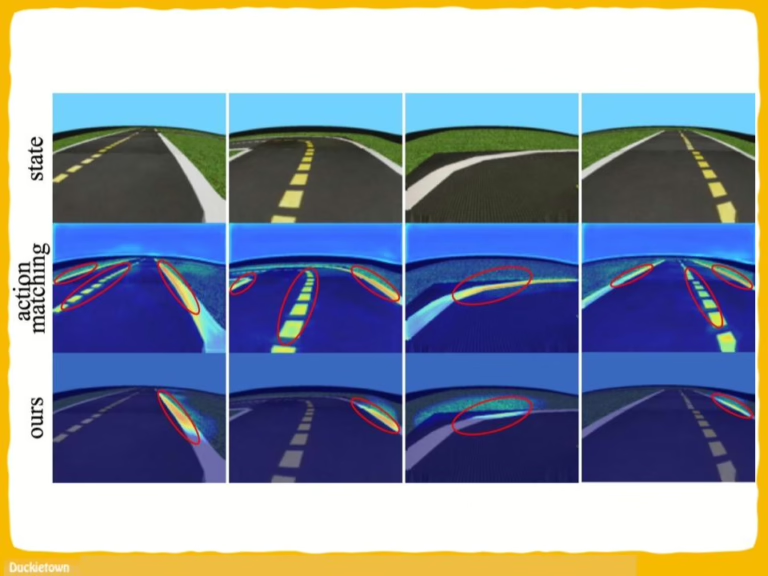
Conclusion
Here are the conclusions from the authors of this paper:
“In this article, we discussed the limitations of the commonly used assumption, the action matching principle, in RL interpretation methods. It is suggested that action matching cannot truly interpret the agent since it differs from the reward-oriented goal of RL. Hence, the proposed method first leverages reward consistency during feature attribution and models the interpretation problem as a new RL problem, denoted as RL-in-RL.
Moreover, it provides an adjustable observation length for one-step reward or multistep reward (or return) consistency, depending on the requirements of behavior analyses. Extensive experiments validate the proposed model and support our concerns that action matching would lead to redundant and noncausal attention during interpretation since it is dedicated to exactly identical actions and thus results in a sort of “overfitting.”
Nevertheless, although RL-in-RL shows superior interpretability and dispenses with redundant attention, further exploration of interpreting RL tasks with explicit causality is left for future work.”
Project Authors
Qisen Yang is an Artificial Intelligence PhD Student at Tsinghua University, China.
Huanqian Wang is currently pursuing the B.E. degree in control science and engineering with the Department of Automation, Tsinghua University, Beijing, China.
Mukun Tong is currently pursuing the B.E. degree in control science and engineering with the Department of Automation, Tsinghua University,
Beijing, China.
Wenjie Shi received his Ph.D. degree in control science and engineering from the Department of Automation, Institute of Industrial Intelligence and System, Tsinghua University, Beijing, China, in 2022.
Guang-Bin Huang is in the School of Electrical and Electronic Engineering, Nanyang Technological University, Singapore.
Shiji Song is currently a Professor with the Department of Automation, Tsinghua University, Beijing, China.
Learn more
Duckietown is a platform for creating and disseminating robotics and AI learning experiences.
It is modular, customizable and state-of-the-art, and designed to teach, learn, and do research. From exploring the fundamentals of computer science and automation to pushing the boundaries of knowledge, Duckietown evolves with the skills of the user.